How Wind Fences Save Millions in Mining: Top 5 Financial Wins from Dust Control
Contents
- Reduced Material Loss – Keeping Profits in Your Wallet
- Reduced Equipment Maintenance – Protecting Your Assets.
- Preserved Product Quality – Preventing Product Devaluation.
- Improve Regulatory Compliance.
- Improved Operational Efficiency.
- Eye on the Bottom Line: The Financial Impact of Wind Fences in Mining.
The mining industry is particularly susceptible to product loss due to dust and wind related events. Profits from mined products are literally blown away in the wind as a result of exposed stockpile storage, large surface areas and the fine particulate content of ore. To add salt to the wound, the assayed value of material in dust found on a mining site is typically three or more times higher than that of the unprocessed material. It goes without saying that those in the industry understand the importance of implementing effective dust suppression strategies to prevent product loss. In 2022, the dust suppression chemicals market in mining was estimated at $3.9B and is expected to almost double by 20321. This value only includes chemical dust suppressants and does not include non-consumable control strategies such as wind fences. With the mining industry’s increasing focus on dust management, wind fences are positioned as a front runner to protect product yield while simultaneously improving environmental compliance and operational efficiency. This blog will explore the top 5 financial benefits of wind fences for the mining industry.
A wind fence, also known as a wind break or wind barrier, is a porous structure that is designed and erected to reduce wind velocity and reduce fugitive dust. They provide financial benefits on mining sites through reduced wind velocity, dust suppression, minimized material loss and preservation of product quality. For detailed information on how a wind fence works visit our website at www.weathersolve.com or speak with our experts directly at info@weathersolve.com or 1-800-749-2201.
Top 5 Financial Benefits of Wind Fences in Mining
1. Reduced Material Loss – Keeping Profits in Your Wallet
Fugitive dust can be generated through pulverization/abrasion of surface material, dust pick up through interaction with turbulent air currents,7 and mechanical processes (dropping from conveyors etc…). On mining sites, a major contributor to the formation of fugitive dust is under-protected stockpiles. Frequent loading of materials, wind currents, spillage and loading equipment traffic at stockpiles also contribute to the generation of unwanted dust. The fine particles emitted from these operations not only lead to health and safety issues for workers, but are also responsible for a tremendous amount of product loss. Winds can significantly impact loosely packed stockpiles where, for example, up to 19% of the heating value of subbituminous coal per year can be lost8. Once the coal is transported to ports, additional product loss can occur from additional wind exposure. Wind protection in the form of custom wind fences reduces these negative impacts both on site and during transport. Wind fences have been shown to reduce fugitive dust by upwards of 80% on mining sites and require no manpower or consumables to operate. Once installed minimal maintenance is required and with the incorporation of a stress release clip system the support structure is protected from failure during extreme weather events. For more information about our stress release clip system read our blog “1:100 Year Storms: Why Wind Fences with Stress Release Clip Systems Make a Difference”.
The return of investment for a wind fence must be underscored. Our real-world example takes us to a large mining operation in the North America with a 7.5-acre coal stockpile. Estimated product losses were reported to be approximately 80,000t of product per annum. The experts at WeatherSolve Structures were tasked with developing a solution to mitigate the huge losses of product that was occurring. A thorough analysis of the source of the potential losses was conducted based on the following:
- RWEQ (Revised Wind Erosion Equation)
- TSP based EPA analysis
- Wind strength/percentage of occurrence
- Wind rose evaluation
- Site topography
- Sieve analysis of soil composition
- Coal pile size and structure
- Other pertinent site-specific data
The results of the engineering study conducted by WeatherSolve on the mine showed that losses were predominantly attributed to stockpile erosion and blow from the conveyor. The study looked at the results determined by the RWEQ wind erosion model as well as the depth of the coal dust that accumulated downwind of the pile. Based on the information, wind fence design and placement was determined to reduce losses due to erosion and airborne particulate matter with a reasonable estimation of 70% reduction leading to approximate cost savings of $1.26M annually.
WeatherSolve custom wind fences have demonstrated fugitive dust reduction of upwards of 90% following installation as illustrated by the real-world results shown in the above graph. Every situation is different, but in most cases a reduction from 50-70% is expected, and any results above 70% are considered good – reduction above 80% is considered great. For context, WeatherSolve wind fences have consistently demonstrated post installation results of +/-5% of the estimated CFD efficacy. Studies conducted in the field corroborate these results. For instance, one study conducted at an Endesa powerplant in Spain showed that a wind fence can reduce annualized coal BTU and mass loss from 26% to 8% per year7.
2. Reduced Equipment Maintenance – Protecting Your Assets.
Equipment maintenance for a typical mining operation account for approximately 30 – 50% of total operating costs10 with the cost of one incident hovering around the $180K mark11. Dust accumulation has been shown to clog filters and engines, decrease equipment efficiency and increase maintenance frequency, repairs and replacement. Although the exact impact has not been studied, wind fences play a critical role in reducing the amount of dust on a mining site and therefore contribute to reducing maintenance frequency and unanticipated breakdowns.
3. Preserved Product Quality – Preventing Product Devaluation
Stockpiles piles are a necessity in the mining industry and cross-contamination is often difficult to navigate especially in a windy environment. One of the culprits causing product devaluation is dust contamination of stockpiles. Dust is insidious and literally creeps around a site being exacerbated by wind and turbulent airflow. The way the dust is transported is dependent on the shape, size and density of the particulate matter. It is carried around a mining site through saltation, repetition creep, short- and long-term suspension with 90% of dust within 1 metre of the ground.
In some environments, as in the case of sulfur piles, the dust can be corrosive wreaking havoc on equipment and resulting in costly damages and potentially dangerous work environments. Our next case for the financial benefits of wind fences in mining takes us to the Atlantic Basin where winds and dust dispersion were causing contaminated stockpiles. The primary objectives for this project were to prevent coke dust (a black sooty substance created during petroleum refining) from corrupting the sulfur production facility, (the sulfur storage area was downwind of the petcoke storage area), reducing erosion of valuable product, and averting contamination of the nearby marine environment.
The environment was highly corrosive because of sulfuric acid, so the challenge was to create a wind fence that would be resistant to extreme corrosion while preserving product quality.
The solution came via a wind/dust fence that separated the two areas and that was entirely made from extremely corrosion resistant materials.
Key features were as follows:
- Kevlar cables coated with PVC, precision produced to length in clean factory conditions.
- Polypropylene wind-fence fabric – which is very chemical resistant.
- Stress-rated nylon attachment clips to reliably secure the fabric to the cables
- Over-sized polished marine grade stainless steel fittings and fastenings where other options were not possible.
- Galvanized and epoxy over-coated steel poles.
The fence also features an inclined upper section. The incline was to improve the control of turbulent vortices around the perimeter that otherwise might have lifted dusty eddies over the fence.
The outcome was a durable and effective fence that could withstand the corrosiveness of the environment while protecting the environment and preserving assets.
4. Improve Regulatory Compliance
Regulatory and governmental bodies around the globe are increasingly vigilant in developing and enforcing policy with respect to environmental protection, air quality and industry standards pertaining to storage, transport and handling of mined materials. For example, the government of British Columbia Mining Health, Safety and Enforcement Division in Canada invested $20M CDN in 2019 to improve regulatory effectiveness in the mining industry within that province15. Hefty fines and penalties are associated with any mining site or organization that is found to be in non-compliance with fines and penalties increasing on the regular. In 2005, the US Mine Safety and Health Administration assessed 116,673 violations in the mining industry doling out approximately $25M USD in fiscal penalties13. Other sources report that $16.6M CDN in penalties were imparted to Canada’s 255 mines between April 2014 and June 201814. Penalties and fines vary in severity and are dependent on the nature and extent of the non-compliance.
There are many contributing factors to regulatory non-compliance ranging from insufficient monitoring and poor operational practices to inadequate infrastructure and resource constraints. When it comes to compliance, reducing fugitive dust can greatly improve adherence in many areas. Improved air quality, worker health and safety and better environmental outcomes are but a few of the ways dust mitigation supports compliance. A custom wind fence is a “set it and forget it” solution for dust control. With no man-power or consumables required for effective dust reduction, wind fences provide a practical and efficient way to improve adherence to statutory requirements potentially saving mining operations from substantial fiscal and legal penalties.
5. Improved Operational Efficiency
Dust wreaks havoc on mining operations contributing to:
- Health and safety issues
- Environmental contamination
- Reduced product quality
- Equipment failure
- Decreased regulatory compliance
These issues detrimentally impact the operations of a mining site contributing to preventable downtime and unnecessary costs. Reduced dust means less time spent on equipment repair and employee absenteeism due to dust related issues. A well-designed, custom wind fence can reduce the amount of fugitive dust by upwards of 80% making for a cleaner, safer, and more productive work site. Wind fences improve operational efficiency by:
- Minimizing Product Contamination – Dust can lead to product contamination from external dust and/or cross contamination from neighbouring stock piles which can detrimentally impact the quality of products. Mitigating dust with a wind fence leads to reduced contamination and improved quality outcomes.
- Decreasing Cleaning and Maintenance Costs – Dust accumulation leads to the necessity for frequent cleaning and site maintenance. These costs can add up quickly and eat into profits and operational budgets. Dust control with a wind fence results in less time spent on cleaning and maintenance activities.
6. Eye on the Bottom Line: The Financial Impact of Wind Fences in Mining
Wind fences consistently demonstrate effective dust mitigation for mining operations around the world leading to significant cost savings and improved operational efficiencies. The financial benefits offered by integrating a wind fence in a dust management plan are obvious. By reducing material loss due to dust, enhancing equipment longevity, preserving product quality, improving regulatory compliance, and boosting overall operational efficiency, wind fences help mining operations protect their bottom line.
Wind fences offer more than just protection from dust; they deliver a return on investment that other solutions simply can’t rival. Once installed, a wind fence continues to operate without manpower or consumables, in good weather and in bad, unlike surface treatments which get scoured off in the first few minutes of an extreme storm and require regular reapplication.
Beyond the tangible benefits of reducing material loss, equipment wear, and regulatory exposure, wind fences also contribute to improved community relations. A wind fence is a dust control solution that visibly reinforces to those around that your operation is proactive and environmentally responsible. For many mining operations, this visible commitment can dramatically improve the comfort factor of nearby communities and improve relationships.
In a world where mining operations are under increasing pressure to optimize output, minimize costs, and improve environmental performance, wind fences are a proven, low-maintenance solution that checks all the boxes. If your mining site is still relying solely on consumables or short-term fixes for dust management, it may be time to invest in a long-term solution that pays dividends: a WeatherSolve wind fence.
References & Reading Materials:
- Allied Market Research Mining Dust Suppression Chemicals Market Research, 2032. https://www.alliedmarketresearch.com/mining-dust-suppression-chemicals-market-A110951 Accessed January 30, 2025
- Nowling, U., “Who Moved my BTUs? The Pitfalls of Extended Coal Storage” Power Magazine December 1, 2016. https://www.powermag.com/who-moved-my-btus-the-pitfalls-of-extended-coal-storage/ Accessed January 31, 2025
- US Bureau of Labor Statistics “Manufacturing and Mining Labor Productivity” https://www.bls.gov/productivity/highlights/manufacturing-mining-labor-productivity.htm Accessed January 31, 2025
- The Mining Association of Canada “The Mining Story 2024: Canadian Mining Industry Facts & Figures”
- Australian Bureau of Statistics “Job Vacancies Australia” https://www.abs.gov.au/statistics/labour/jobs/job-vacancies-australia/latest-release Accessed January 30, 2025
- NIOSH 2008 Work related lung disease surveillance report, 2007. Morgantown, WV: US Department of Health and Human Services, CDC, DHHS (NIOSH) Publication No. 2008143a
- Cowherd, C., Axetell, K., Guenther, C., et al “Development of Emission Factors for Fugitive Dust Sources” US Environmental Protection Agency PA June 1974.
- Baruya, P., “Losses in the Coal Supply Chain” IEA Clean Coal Centre December 2012
- Hat Creek Project Mining Feasibility Report Appendix C Fugitive Mine-Dust Study by Cominco-Monenco Joint Project 1979
- Mining Digital “Implementing Effective Maintenance Strategies for Long Term Production Goals” May 17, 2020 https://miningdigital.com/supply-chain-and-operations/implementing-effective-maintenance-strategies-long-term-production-goals Accessed February 4, 2025
- Mining Digital “How-To: Combat Unplanned Equipment Downtime” May 17, 2020 https://miningdigital.com/digital-mining/how-combat-unplanned-equipment-downtime Accessed February 4, 2025
- Nowling, U. “Who Moved My BTUs? The Pitfalls of Extended Coal Storage” Power Magazine Dec 2016
- US Dept of Labor Mine Safety & Health Administration “Regulatory Economic Analysis for Criteria & Procedures for Proposed Assessment of Civil Penalties: Final Rule” March 2007
- Linnitt, Carol. “Major gaps in mining regulations flagged in environment commissioner’s report” The Narwhal. April 3, 2019. Accessed February 18, 2025.
- Government of BC “Mining Compliance and Enforcement” https://www2.gov.bc.ca/gov/content/industry/mineral-exploration-mining/compliance-enforcement Accessed February 19, 2025
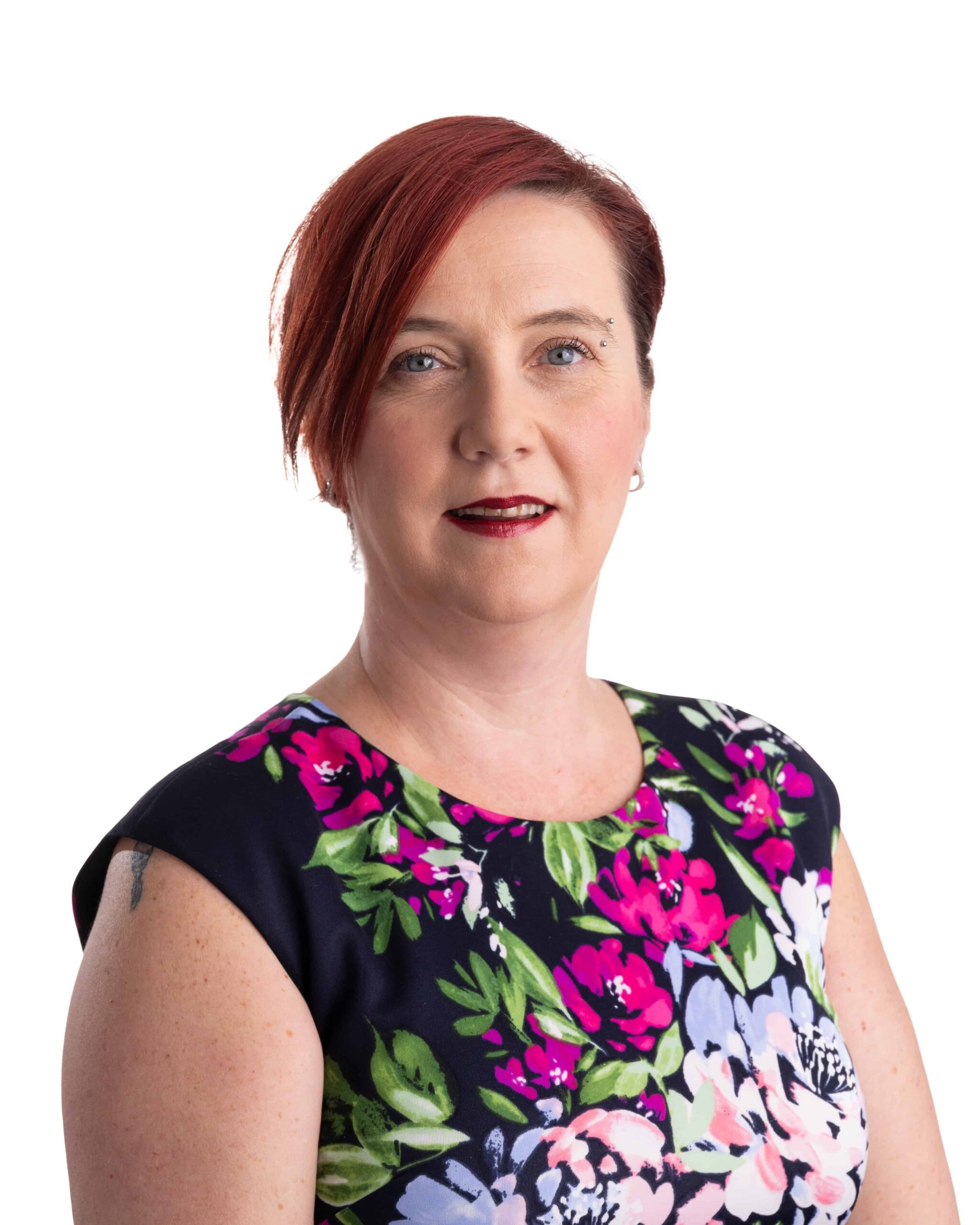
Claire Cowie is a seasoned Quality Assurance Manager with over two decades of experience in healthcare and manufacturing. Her career began in pharmacy, where she led teams and honed her skills in quality management systems. As she transitioned to the manufacturing sector, her unique background combines a deep understanding of policy and quality assurance with a keen eye for quality control.
Claire has been instrumental in implementing and cultivating a comprehensive quality control program within WeatherSolve Structures. She has successfully integrated her pharmaceutical background with manufacturing best practices, particularly in areas such as Good Manufacturing Practices (GMP) and ISO 9001 standards. Her unique blend of experience continues to drive innovation and excellence in her role.